Competency Acceptance Test (CAT)
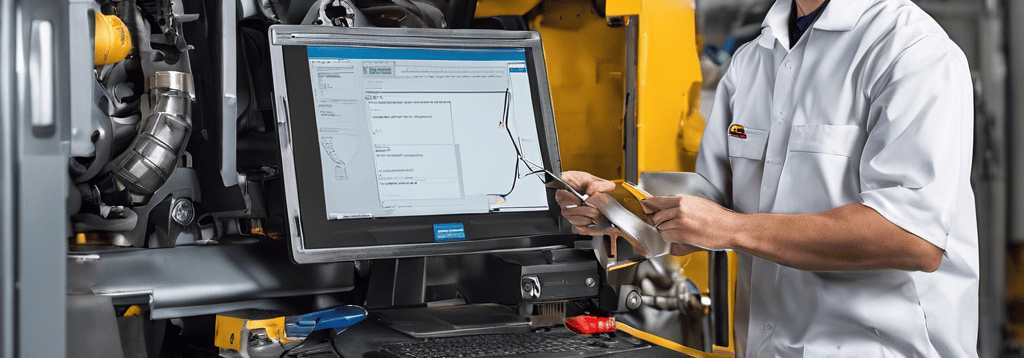
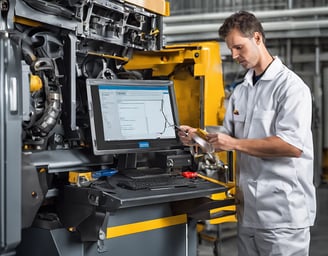
Machine Reactive Maintenance
About Machine Reactive Maintenance
Reactive maintenance, also known as breakdown maintenance, is a strategy of repairing equipment and systems only when they fail. Unlike preventive or predictive maintenance, which aims to avoid or foresee failures, reactive maintenance responds to actual failures as they occur.
For example, if a machine stops working unexpectedly, a reactive maintenance approach would involve diagnosing the problem and then fixing it so the machine can be brought back into operation.
While reactive maintenance can sometimes be seen as less desirable due to the unplanned downtime and potential for increased costs (from emergency repairs or overtime), there are scenarios where it can be a valid strategy. For instance, on non-critical or redundant systems, or on equipment that's inexpensive or easy to replace, a reactive maintenance strategy may be more cost-effective.
However, in most industrial or manufacturing settings, relying solely on reactive maintenance is not ideal. Unplanned downtime can be costly and disruptive, and equipment can often be damaged further when it's run to the point of failure. Therefore, a mixed approach is often best, with predictive or preventive maintenance used on critical or costly equipment, and reactive maintenance reserved for non-critical or less costly items.
In terms of certification for competency in reactive maintenance, it would likely focus on skills like problem diagnosis, quick and effective repair methods, safety during emergency repair work, and communication skills for reporting issues and actions taken.
Competency Acceptance Test (CAT) for Machine Predictive Maintenance Content
Providing certification for competency in machine reactive maintenance is a great way to ensure individuals have the necessary knowledge and skills to perform these crucial tasks effectively. Below is the test content:
Understanding of Machine Operation:
Test taker should demonstrate a solid understanding of the basic operation of the machine, identify its main components, and understand their functions.
Diagnosis of Machine Issues:
This could be done by creating a simulated machine failure. The test taker would need to investigate the problem, identify the cause of the failure, and propose a solution. This section could include a variety of potential problems, such as mechanical breakdowns, electrical failures, or software errors.
Performing Reactive Maintenance Tasks:
The test taker should demonstrate their ability to safely and effectively perform the necessary repair tasks. This could include replacing broken or worn-out components, fixing electrical issues, or adjusting software settings. This should be done following appropriate safety protocols.
Usage of Tools and Equipment:
The candidate should demonstrate their ability to use typical tools and equipment for repair work, such as wrenches, screwdrivers, multimeters, and diagnostic equipment.
Communication and Reporting:
The candidate should demonstrate their ability to clearly and accurately report on the issue they encountered, the steps they took to diagnose and repair it, and any recommendations for future action to prevent a recurrence of the problem. 6. Working under Pressure: Since reactive maintenance often involves unexpected breakdowns and time pressure, the test could also assess the candidate's ability to work effectively under these conditions.
These tests shall be conducted under safe conditions, with appropriate supervision and protective equipment.
READY TO TAKE A TEST ?
YES
NOT YET

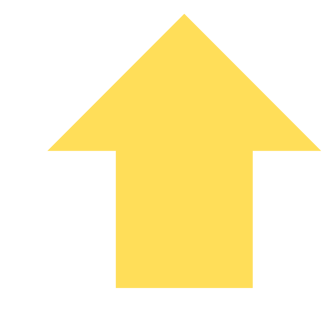

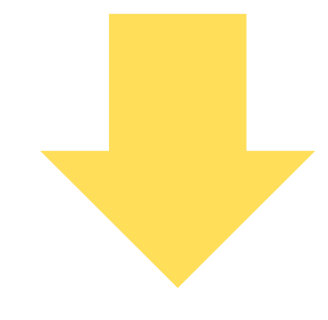