Competency Acceptance Test (CAT)
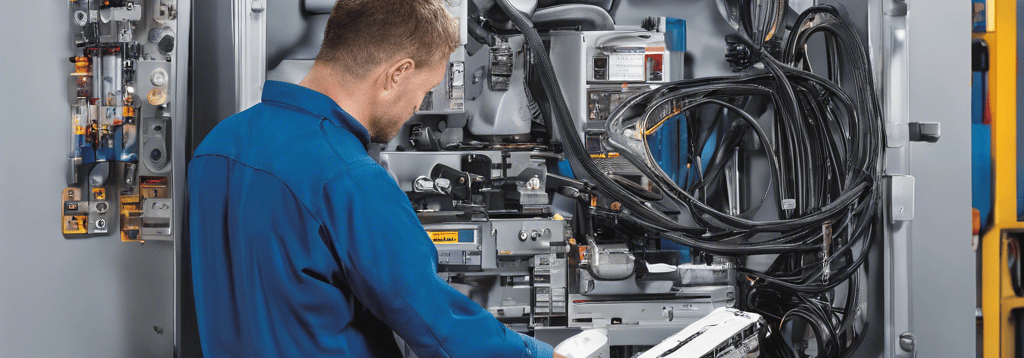
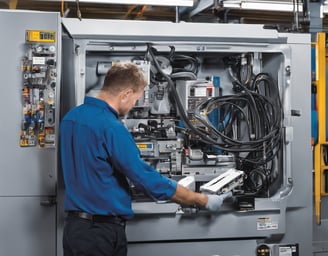
Machine Corrective Maintenance
About Machine Corrective Maintenance
Corrective maintenance, also known as remedial or improvement maintenance, refers to the set of tasks performed to identify, isolate, and rectify a fault so that the failed equipment, machine, or system can be restored to an operational condition. In simple terms, it's the process of fixing things that are broken or not working properly.
Corrective maintenance can be both planned and unplanned:
1. Planned Corrective Maintenance:
This occurs when an issue is identified during a routine inspection or preventive maintenance but does not require immediate attention. The repair is then scheduled and performed at a later time that causes minimal disruption to the operation.
2. Unplanned Corrective Maintenance:
This is often equated to reactive or breakdown maintenance because it occurs when an unexpected failure happens, and immediate action is required to restore the machine to its operational condition.
Improvement maintenance is a bit different, and it typically refers to actions taken to improve the performance or extend the useful life of a machine or system beyond its current state. This could include replacing worn-out parts before they fail, upgrading old or obsolete components, or implementing more efficient or modern technology.
When it comes to competency in corrective maintenance, the focus would likely be on skills like problem diagnosis, carrying out effective repairs, safety during maintenance work, and decision-making skills for determining when and how to perform corrective actions. For improvement maintenance, it would involve understanding machine performance, knowledge of newer technologies or parts that can improve performance, and skills to implement these improvements.
Improvement maintenance, sometimes also known as modification or upgrade maintenance, refers to the set of tasks performed to improve the functionality, efficiency, or lifespan of an existing machine or system. It's a proactive strategy intended to enhance performance or extend useful life beyond its current state, rather than just maintaining or restoring the existing state of the equipment.
Improvement maintenance may include tasks such as:
1. Replacing components with more modern or higher-performance versions: For instance, an old mechanical part might be replaced with a newer, more efficient design, or an old piece of electronics might be replaced with a more modern and powerful version.
2. Modifying systems or procedures to improve efficiency: This might include changes to the way the machine is operated, the implementation of more efficient maintenance procedures, or changes to the working environment of the machine to reduce wear and tear.
3. Implementing new technology to enhance functionality: For example, installing sensors to monitor machine health in real-time, upgrading software to a version with more features, or implementing automation systems to reduce manual intervention.
4. Making changes to improve safety or ergonomics: This could involve adding safety features, changing the layout or setup of a machine to make it more user-friendly, or implementing features to reduce noise, vibration, or other environmental factors.
The goal of improvement maintenance is not only to keep the machine running but to make it run better than before. This can lead to significant benefits in terms of productivity, cost savings, worker satisfaction, and product quality. It requires a deep understanding of the machine or system, the ability to identify potential improvements, and the skills to implement those improvements effectively.
Competency Acceptance Test (CAT) for Machine Corrective Maintenance Content
Providing certification for competency in machine corrective or improvement maintenance is a great way to ensure individuals have the necessary knowledge and skills to perform these crucial tasks effectively. Below is the test content:
Understanding of Machine Operation and Performance:
Test takers should demonstrate a strong understanding of how the machine functions, what its performance specifications are, and what factors may affect its performance.
Identification of Improvement Opportunities:
Test takers should be able to identify areas where the machine's performance could be improved. This might involve identifying outdated or inefficient components, recognizing inefficient operating procedures, or noting environmental factors that could be optimized for better performance.
Planning and Implementing Improvements:
Test takers should demonstrate the ability to plan and carry out improvement projects. This could involve selecting suitable replacement components, designing modifications to the machine or its environment, or planning changes to operating procedures. They should be able to explain why they have chosen a particular course of action and how they expect it to improve the machine's performance.
Safety Considerations:
Any proposed improvements should not compromise the safety of the machine or its operators. Test takers should be able to explain how they have taken safety into account when planning their improvements.
Performance Testing:
After implementing their improvements, test takers should carry out tests to measure the performance of the machine and demonstrate the effectiveness of their improvements.
Reporting:
Test takers should provide a written or verbal report explaining the improvements they made, the reasons for these improvements, and the results of their performance tests.
These tests shall be conducted under safe conditions, with appropriate supervision and protective equipment.
READY TO TAKE A TEST ?
YES
NOT YET

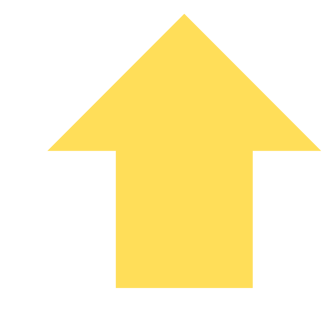

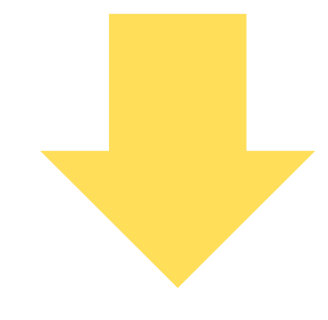